Il confezionamento del calcestruzzo consiste nell'impasto dei componenti (leganti, aggregati e acqua) opportunamente dosati per ottenere la resistenza richiesta. Alla buona riuscita del processo contribuiscono l'immagazzinamento, la dosatura e la miscelazione dei componenti.
IMMAGAZZINAMENTO DEL CALCESTRUZZO (cemento) E DEGLI AGGREGATI (inerti)
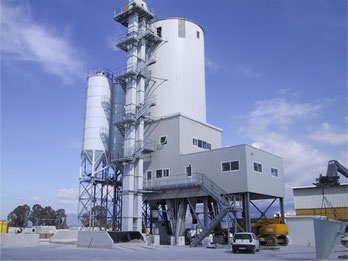
Il cemento può essere conservato in sacchi o in silos, quest'ultima soluzione è adatta nel caso dei grandi impianti di produzione di calcestruzzo. E' molto importante che il calcestruzzo sia accuratamente protetto dall'umidità e che sia utilizzato ancora fresco, cioè non deve stazionare troppo a lungo in cantiere.
Gli aggregati possono essere depositati in mucchi a terra, divisi in base alle varie classi granulometriche, oppure in silos (o tramogge), o nelle classiche centrali di betonaggio.
DOSATURA DEI COMPONENTI DEL CALCESTRUZZO
Partiamo dicendo che i componenti principali sono gli aggregati. Gli aggregati, o inerti, sono una larga categoria di materiali minerali granulari particellari grezzi usati nelle costruzioni. Possono essere naturali, artificiali o riciclati da materiali precedentemente usati nelle costruzioni. Principalmente sono la ghiaia, la sabbia, l'argilla espansa, la vermiculite e la perlite.
In un conglomerato rappresentano la sua ossatura, in cui la coesione è assicurata dalla calce, o in alternativa dal bitume o pasta cementizia.
Nei conglomerati cementizi, gli aggregati non partecipano all'indurimento del calcestruzzo, ma operano un ruolo fondamentale sulle caratteristiche meccaniche del calcestruzzo, in base alla loro qualità. Rivestono un ruolo fondamentale anche per la loro quantità, infatti nella massa di un calcestruzzo costituiscono all'incirca l'80% del peso.
Gli aggregati, o inerti, naturali adoperati per il confezionamento dei calcestruzzi sono costituiti da:
- ghiaie e sabbie alluvionali estratte da letti di fiume o da cave;
- pietrischi o sabbie provenienti dalla frantumazione di rocce.
La loro forma dipende sopratutto dalla loro origine:
- quelli di origine fluviale sono più o meno arrotondati e lisci;
- quelli frantumati hanno spigoli vivi ed irregolari.
La qualità di un aggregato dipende in buona misura dalla sua natura petrografica e quindi dalla composizione mineralogica e dalle proprietà fisiche e chimiche che ne derivano. Da non trascurare, in quanto riveste un ruolo fondamentale nella qualità del calcestruzzo, è la composizione granulometrica (curva granulometrica degli inerti).
La dosatura degli aggregati (o inerti) può essere effettuata nei modi seguenti:
- dosatura in volume, che è un metodo semplice ed economico, infatti richiede solamente dei contenitori opportunamente dimensionati, o in alternativa anche una semplice carriola. Lo svantaggio è che in questo modo potrebbero verificarsi dosature poco precise, a causa delle variazione di volume che subiscono gli aggregati (in special modo la sabbia) per il variare del tenore di umidità contenuta e per l'assestamento;
- dosatura in peso, si tratta di un procedimento più affidabile, praticato usualmente nei cantieri meglio equipaggiati, perchè basato sull'impiego di specifiche bilance. Fondamentale, però, che le pesate avvengano a parità di condizione del materiale, cioè a tenori costanti di umidità degli aggregati.
MISCELAZIONE DEI COMPONENTI DEL CALCESTRUZZO
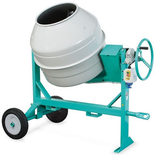
La miscelazione, o impasto, dei componenti avviene utilizzando vari tipi di betoniere, o in alternativa ricorrendo a dei veri e propri impianti di betonaggio. Il tipo di attrezzatura più adatta per la miscelazione deve essere scelta in base al tipo di lavoro e sopratutto alla quantità di calcestruzzo da realizzare.
CONSISTENZA DEI GETTI DI CALCESTRUZZO DEGLI ELEMENTI STRUTTURALI
La consistenza dei getti di calcestruzzo è un parametro fondamentale per la buona riuscita delle strutture di calcestruzzo armato, perchè è direttamente rapportata alla composizione e alla lavorabilità dell'impasto. Infatti, è bene determinare accuratamente la consistenza come una delle prime fasi, in base al tipo di lavoro da eseguire, le attrezzature da impiegare per gli impasti, quali mezzi di trasporto impiegare, dalla posizione e anche dalle dimensione che dovranno avere i getti.
Ad esempio in caso di un getto che presenti difficoltà di costipazione, con un'armatura metallica molto stretta e con sezione stretta la consistenza del getto dovrà forzatamente essere piuttosto fluida. Invece, un getto che avverrà in posizione inclinata (come può avvenire in uno scivolo) il getto, affinchè non scivoli verso il basso, la consistenza dovrà essere plastica o umida.
Di norma si seguono i seguenti principi:
Tipo di costruzione | Abbassamento al cono (slump)^1[mm] | Classe di consistenza | Denominazione corrente |
Costruzioni massicce | 10/40 mm | S1 | umida |
Fondazioni e pavimentazioni | 50/90 mm | S2 | plastica |
Elementi comuni in calcestruzzo | 100/150 mm | S3 | semifluida |
Elementi sottili e/o con armatura molto fitta | 160/200 mm | S4 | fluida |
Elementi sottili e/o con armatura molto fitta in situazioni particolari | >210 mm | S5 | superfluida |
Per meglio comprendere la tabella di sopra è obbligatoria una spiegazione in merito alla prova di abbassamento al cono, anche detta Slump Test o Cono di Abrams.
Questo test serve ad indicare se l'impasto per il calcestruzzo che si è ottenuto rientri nelle varie categorie: umido, plastico, semifluido, fluido e superfluido. Infatti, ad ognuno di essi corrisponde una specifica classe di consistenza che, così come previsto dalle norme UNI EN 12350-2, UNI EN 206-1 e UNI 11104, indicano per quale tipo di costruzione quello specifico impasto può essere adoperato.
Passiamo a spiegare come viene svolto il test:
Prima di tutto occorre indicare che gli aggregati non devono avere una dimensione massima superiore a 40 mm.
Fondamentale per eseguire il test è uno stampo in metallo dalla forma conica, realizzato con un materiale che non sia aggredibile dalla pasta cementizia, come la lamiera di acciaio inossidabile o zincato, con spessore minimo di 1,5 mm. E', inoltre, molto importante sincerarsi che il suo interno sia liscio e privo di sporgenze, come chiodature o ammaccature.
Le dimensioni interne dello stampo del cono sono le seguenti:
- diametro della base inferiore: 200 mm (con tolleranza ± 2 mm);
- diametro della base superiore: 100 mm (con tolleranza ± 2 mm);
- altezza: 300 mm (con tolleranza ± 2 mm).
Le basi inferiori e superiori sono aperte e formano angoli retti con l'asse del cono.
Lo stampo è dotato di due manici, posti a 2/3 dell'altezza nella porzione superiore, per la sformatura e, nella parte inferiore, di ganci di fissaggio o di staffe che servono a mantenerlo fermo con i piedi nel corso del riempimento. Nel caso in cui si adoperino i ganci di fissaggio ci si deve accertare che lo sblocco possa avvenire senza provocare alcun movimento nello stampo.
Come già detto il test valuta la deformazione che l'impasto subisce per effetto del proprio peso, quando viene privato del recipiente che lo sostiene.
FASE 1) la prima fase consiste nell'inumidire lo stampo e porlo su di una superficie rigida, liscia, umida e non assorbente;
FASE 2) la seconda fase consiste nel riempimento del cono, assicurandosi di mantenerlo immobile. Il cono dovrà essere riempito con molta rapidità, con l'ausilio di una cazzuola o sessola, con tre strati successivi assestati, ciascuno dei quali pari a circa 1/3 dell'altezza del cono.
Di base ogni strato si costipa con circa 25 colpi, eseguiti con un pestello (che deve rispettare le dimensioni di lunghezza 2'= 61cm, diametro 2/3"=1,6 cm con punta arrotondata) uniformando l'impasto sull'intera sezione orizzontale.
Un accorgimento importante è dato in merito allo strato inferiore, infatti in questo caso la metà dei colpi deve essere data a spirale lungo il perimetro del cono, tenendo il pestello leggermente inclinato e facendolo penetrare per tutta la profondità dello strato. Per quanto riguarda gli altri due strati, il penetramento dovrà essere solo leggermente superiore al loro spessore.
Non appena sarà stato assestato anche l'ultimo strato, dovrà essere aggiunto ulteriore calcestruzzo per compensare l'abbassamento di livello del conglomerato, causato dal costipamento, al di sotto del bordo superiore.
FASE 3) Lisciare la superficie del calcestruzzo con il pestello, svolgendo i movimenti a sega e di rotolamento. Successivamente rasare e ripulire la superficie di appoggio dal calcestruzzo che può esservi caduto di sopra. Adesso è necessario rimuovere lo stampo, in non più di 5/10 secondi, sollevandolo con molta attenzione (è di fondamentale importanza non provocare alcun movimento laterale o di torsione nel calcestruzzo).
Tutte e 3 le fasi devono essere ultimate in non più di 150 secondi.
FASE 4) misurazione dello slump: da eseguire immediatamente dopo la rimozione dello stampo, viene eseguita misurando l'abbassamento al cono, come differenza fra l'altezza nominale dello stampo (hm = 300 mm) e quella del punto più alto del calcestruzzo impastato (hs), arrotondando ai 10 mm più prossimi. S = hm - hs
Da questa misura si evince la classe di consistenza dell'impasto.
Attenzione però, l'unico abbassamento accettabile è quello regolare (si abbassa semplicemente), tutti gli altri, come abbassamento di taglio o collasso, implicano qualche irregolarità nell'impasto del calcestruzzo. Se invece al primo tentativo si ottiene un abbassamento per scorrimento (il calcestruzzo si disgrega in alcune sue parti), la prova deve essere ripetuta, se il problema si verificherà nuovamente sarà da scartare tutto il calcestruzzo perchè non idoneo al test.
Questo test non è valido in caso di calcestruzzo autolivellante, poichè la sua fluidità è così alta da rendere irrilevante il test.
DIAMETRO MASSIMO DEGLI AGGREGATI
Le norme prescrivono che si deve dosare la composizione del getto in modo da evitare il rischio di segregazione o la formazione di nidi di ghiaia e da ridurre l'entità delle deformazioni differite, definendo il valore del diametro massimo degli inerti in base allo spessore delle nervature e dalla distanza tra le armature.
Le regole generali quando si deve determinare il diametro massimo degli aggregati sono i seguenti:
- non superare 1/4 della dimensione minima del getto;
- sia minore di 5 mm dell'interferro dell'armatura, ad eccezione del caso in cui si raggruppino le barre o si usino altri accorgimenti;
- non superi del 30% lo spessore del copriferro.
Una tabella esemplificativa:
Dimensione minima della sezione dell'elemento strutturale (in cm) | Dimensione massima degli aggregati per tipi di opere (in cm) | |||
pareti armate, pilastri e travi | pareti non armate | lastre molto armate | lastre poco armate | |
8/15 | 1,5/2 | 2 | 2/2,5 | 2/3,5 |
16/30 | 2/4 | 4 | 4 | 4/7,5 |
31/75 | 4/7 | 7 | - |
IL CALCESTRUZZO PRECONFEZIONATO
Il calcestruzzo può essere fornito già preconfezionato da ditte specializzate mediante autobetoniere. Lo scarico viene eseguito grazie ad apposite canalette, che sono impiegate quando la cassaforma è posizionata ad una quota più bassa dell'autobetoniera, o in alternativa con pompe montate sull'autocarro (le autopompe), in caso siano necessari getti da effettuare ad una quota superiore o se vi siano casseforme di particolare conformazione oppure di difficile accesso.
Il calcestruzzo preconfezionato ha particolari vantaggi in specifici lavori o situazioni, come:
- getti in cantiere con aree inadeguate all'immagazzinamento dei materiali e al confezionamento degli impasti;
- getti di notevole quantità, eseguiti in lotti scaglionati nel tempo in parti del cantiere distanti tra loro, che rendono poco economico un impianto fisso;
- getti imprevisti e urgenti;
- quando sono richieste grandi quantità di calcestruzzo in breve tempo per non interrompere la continuità dei getti.
Altri articoli correlati:
Il calcestruzzo a vista o faccia a vista
armatura metallica e disarmo delle casseforme del calcestruzzo armato
getti di calcestruzzo effettuati a basse temperature
stagionatura e maturazione accelerata del calcestruzzo
calcestruzzo e calcestruzzo armato - trasporto, getto e costipamento del getto nelle casseforme
Le casseforme per il getto del calcestruzzo armato - casseforme in legno e casseforme metallica
Il calcestruzzo armato (cemento armato) - cos'è e le sue caratteristiche principali
Scrivi commento